Industrial LT Control Panel Manufacturers
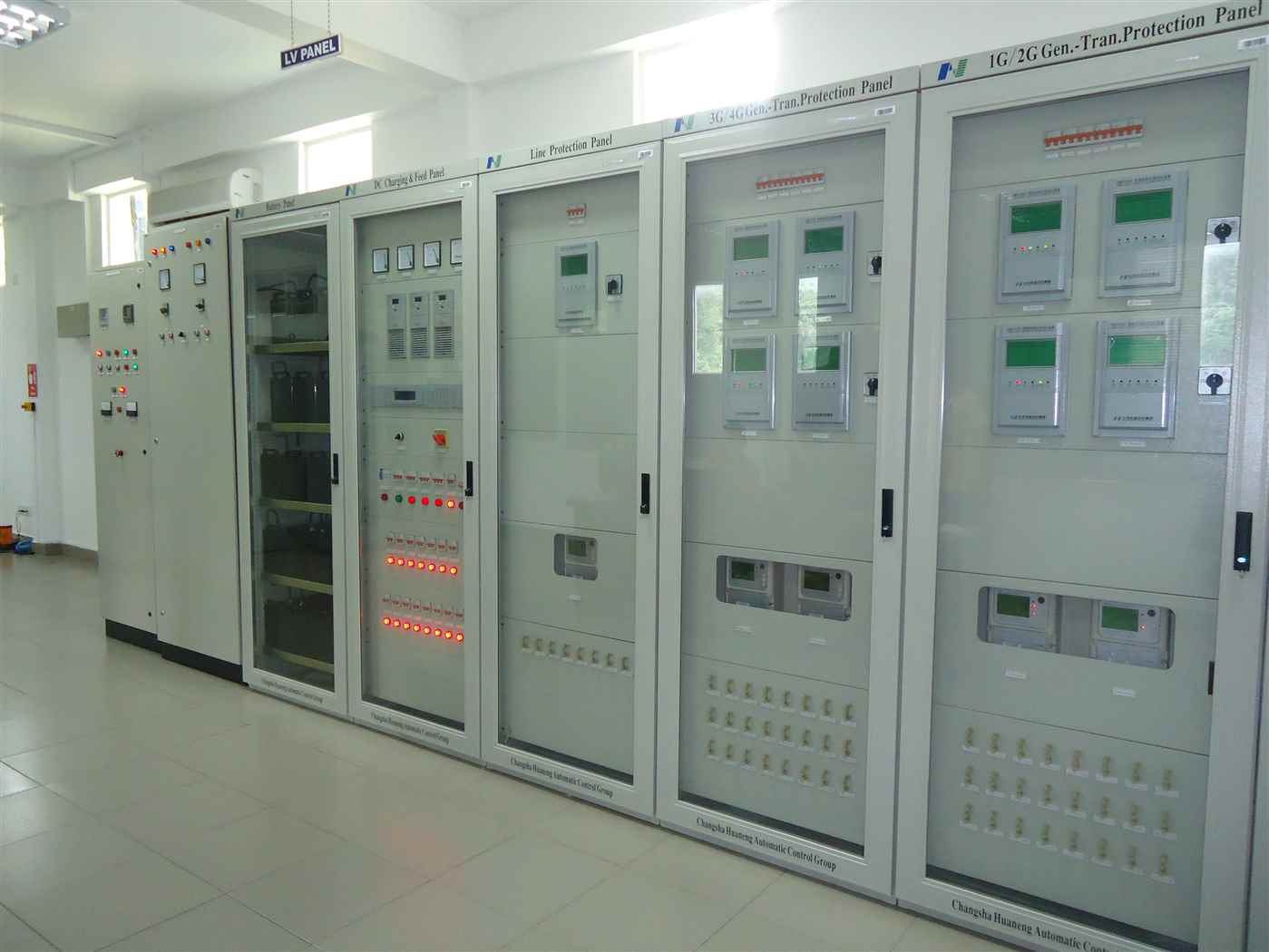
Industrial LT Control Panel Manufacturing
Industrial Low Tension (LT) control panels are essential components in electrical distribution systems across various industries. They serve to control, protect, and monitor electrical systems, ensuring their safe and efficient operation. The manufacturing process of LT control panels involves several critical stages, including design, assembly, testing, and quality control. Here’s an in-depth look at the process of manufacturing LT control panels.
1. Design and Specification
The first step in manufacturing an LT control panel is detailed design and specification. This involves understanding the specific needs of the client, including the type of machinery or processes the panel will control. Engineers and designers work closely with clients to gather information about electrical requirements, load capacities, safety standards, and any special features needed.
Design software is used to create detailed schematics and layouts for the control panel. This includes specifying the types of components required, such as circuit breakers, contactors, relays, and programmable logic controllers (PLCs). The design must adhere to national and international electrical standards and safety regulations to ensure reliability and compliance.
2. Material Selection
Once the design is finalized, the next step is selecting the appropriate materials. High-quality materials are crucial for the durability and performance of the control panel. Common materials used in manufacturing include:
- Enclosures: Typically made from steel or stainless steel, enclosures protect the internal components from environmental factors such as dust, moisture, and mechanical damage.
- Busbars: Made from copper or aluminum, busbars are used to conduct electricity within the panel.
- Wiring and Cables: High-grade insulated cables are used for connecting various components.
- Components: Circuit breakers, switches, relays, and PLCs are selected based on the panel’s design specifications.
3. Assembly
The assembly process involves several key steps:
- Enclosure Preparation: The metal enclosure is prepared by cutting and drilling holes for mounting components, ventilation, and cable entry. It may also be painted or coated for additional protection.
- Component Mounting: Components such as circuit breakers, contactors, and PLCs are mounted on the panel’s backplate or din rail. Proper spacing and alignment are crucial to ensure easy access and maintenance.
- Wiring: Electrical wiring is done according to the design schematics. This involves connecting various components and ensuring that all connections are secure and properly insulated.
- Control Circuit Assembly: Control circuits, including relays and timers, are assembled and wired according to the control logic designed for the panel.
4. Testing
Testing is a critical phase in the manufacturing process to ensure the control panel operates correctly and safely. Several tests are performed, including:
- Visual Inspection: Checking for any obvious defects or errors in wiring and component placement.
- Insulation Resistance Testing: Ensuring that insulation resistance meets the required standards to prevent electrical leakage or short circuits.
- Functional Testing: Verifying that the panel operates as intended, including testing all control and protection features.
- Load Testing: Simulating the panel’s operation under actual load conditions to ensure it performs reliably.
5. Quality Control
Quality control is an ongoing process throughout the manufacturing of LT control panels. It involves:
- Adherence to Standards: Ensuring that all components and assembly processes meet national and international electrical standards.
- Documentation: Maintaining detailed records of design specifications, materials used, and test results. This documentation is crucial for traceability and future reference.
- Final Inspection: A thorough final inspection is conducted to ensure the control panel is free from defects and meets all design requirements before it is dispatched to the client.
6. Integration and Commissioning
After manufacturing and quality control, the LT control panel is ready for integration and commissioning at the client’s site. This involves:
- Installation: Proper installation of the panel in its designated location, ensuring it is securely mounted and connected to the electrical system.
- Configuration: Configuring the control panel’s settings to match the specific requirements of the client’s system.
- Testing: Conducting final tests at the site to verify that the panel functions correctly within the actual operating environment.
7. Maintenance and Support
Post-installation support and maintenance are essential for ensuring the long-term reliability of LT control panels. This includes:
- Regular Inspections: Scheduled inspections and maintenance to identify and address any potential issues before they become serious problems.
- Technical Support: Providing technical assistance and troubleshooting in case of any operational issues or malfunctions.
Conclusion
The manufacturing of industrial LT control panels is a complex and meticulous process that requires careful attention to design, materials, assembly, and testing. By adhering to high standards of quality and safety, manufacturers ensure that these control panels provide reliable and efficient operation for various industrial applications. The final product not only meets the immediate needs of the client but also contributes to the overall safety and efficiency of the industrial electrical systems.