Outdoor Electrical Panels Manufacturer
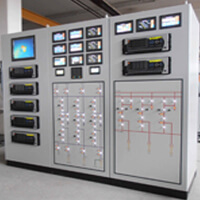
Contact : +91 99005 84314
Outdoor Electrical Panels: Manufacturing Overview
Outdoor electrical panels are essential components in modern electrical systems, providing a crucial interface for managing and controlling electrical power distributed across various applications. The manufacturing of these panels involves a combination of engineering precision, material science, and stringent quality controls to ensure reliability, safety, and durability.
1. Design and Specifications
The manufacturing process of outdoor electrical panels begins with detailed design and engineering. These panels are designed to house circuit breakers, switches, and other electrical components in a way that ensures optimal performance and safety. The design phase involves:
- Load Requirements: Understanding the electrical load and operational requirements is crucial. This includes voltage, current, and the type of electrical equipment to be housed.
- Environmental Considerations: Outdoor panels must be designed to withstand environmental conditions such as temperature extremes, moisture, dust, and UV radiation. This often involves selecting appropriate materials and coatings.
- Safety Standards: Compliance with national and international safety standards such as IEC (International Electrotechnical Commission) or ANSI (American National Standards Institute) is mandatory. These standards govern aspects like insulation, grounding, and protection against electrical faults.
2. Material Selection
Materials used in the manufacturing of outdoor electrical panels must offer durability and protection against harsh conditions. Common materials include:
- Steel: Often used for its strength and rigidity, steel panels are typically coated with anti-corrosive treatments like powder coating or galvanization to resist weathering.
- Aluminum: Known for its lightweight and corrosion-resistant properties, aluminum is often used in environments prone to high humidity.
- Fiberglass: This material is used for its excellent resistance to corrosion, making it suitable for highly corrosive environments.
- Polycarbonate: For certain applications, high-strength polycarbonate panels are used due to their impact resistance and durability.
3. Fabrication and Assembly
Once the materials are selected, the fabrication process begins. This involves several steps:
- Cutting and Shaping: Sheets of metal or other materials are cut to size and shaped using techniques like stamping, laser cutting, or water jet cutting. Precision is key to ensure that the components fit together accurately.
- Welding and Joining: Metal panels are often welded or bolted together. For aluminum or fiberglass panels, adhesives or mechanical fasteners may be used.
- Sealing and Insulation: To protect the internal components from environmental factors, seals are applied around doors and joints. Insulation materials are used to prevent electrical shock and maintain thermal regulation.
4. Component Integration
Outdoor electrical panels house a variety of components that need to be carefully integrated:
- Circuit Breakers and Switches: These components are mounted onto the panel’s interior and connected according to the design specifications.
- Wiring and Connections: Proper wiring practices are critical to ensure safe and reliable operation. Wires are routed through conduits or cable trays, and connections are made using terminals or connectors.
- Control Systems: For more advanced panels, control systems like programmable logic controllers (PLCs) or remote monitoring devices may be installed to allow for automated operation and diagnostics.
5. Quality Control
Quality control is a vital part of the manufacturing process. Various tests and inspections are performed to ensure the panels meet the required standards:
- Electrical Testing: Panels are tested for electrical safety, including insulation resistance, continuity, and functionality of circuit breakers and switches.
- Environmental Testing: Panels may undergo tests for resistance to moisture, dust, and extreme temperatures. This ensures they can operate reliably under actual environmental conditions.
- Visual Inspection: A thorough visual inspection checks for defects in materials, workmanship, and assembly.
6. Certification and Compliance
To ensure that outdoor electrical panels meet safety and performance standards, they must be certified by relevant authorities. This could include:
- UL Certification: In the United States, panels often need Underwriters Laboratories (UL) certification, which verifies that the product meets safety and performance standards.
- CE Marking: In Europe, CE marking indicates compliance with European health, safety, and environmental protection standards.
- ISO Certification: International Organization for Standardization (ISO) certification may be required to demonstrate adherence to quality management systems.
7. Final Assembly and Testing
Once all components are assembled and integrated, the final product undergoes a comprehensive testing process. This includes:
- Functional Testing: Ensuring that all electrical functions, such as switching and circuit protection, operate correctly.
- Environmental Testing: Reconfirming that the panel can withstand the environmental conditions it is designed for.
- Field Testing: In some cases, panels are tested in actual field conditions to validate performance under real-world scenarios.
8. Packaging and Delivery
After successful testing, the panels are packaged for delivery. Packaging must protect the panel from damage during transportation and handling. This includes:
- Protective Wrapping: Using materials like shrink wrap or bubble wrap to shield the panel.
- Labeling: Clearly labeling the packaging with information about the panel, including its specifications and any handling instructions.
- Shipping: Panels are then shipped to their destination, ready for installation and use.
Conclusion
The manufacturing of outdoor electrical panels involves a complex interplay of design, material selection, fabrication, and rigorous testing. Each step is crucial to ensure that the panels can perform reliably and safely in diverse and often challenging outdoor environments. By adhering to high standards and utilizing advanced manufacturing techniques, producers can deliver high-quality electrical panels that meet the demands of modern infrastructure.