Outdoor Electrical Panels Manufacturers Near Peenya
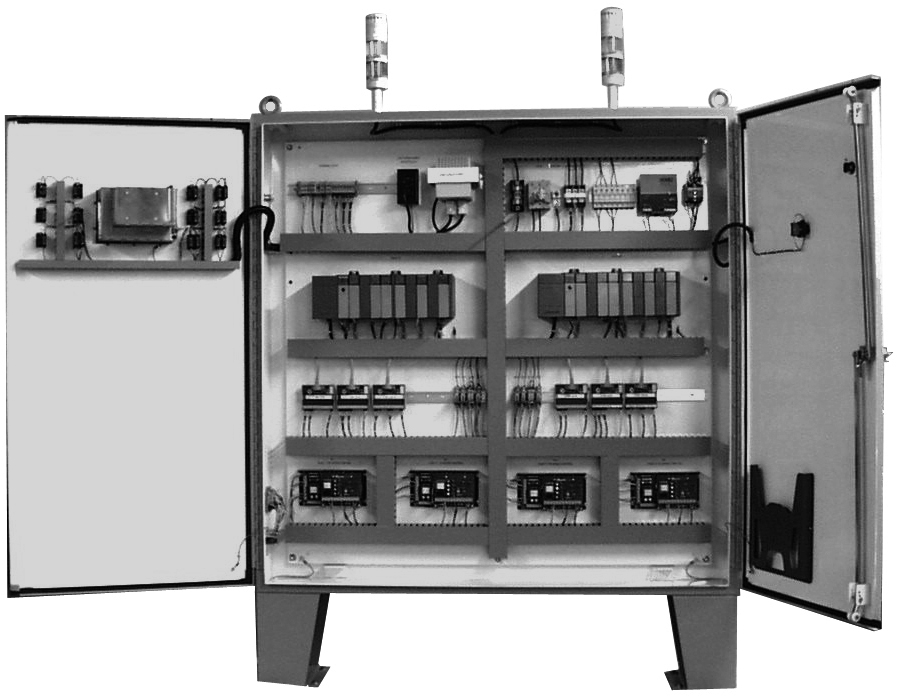
Contact : +91 99005 84314
Outdoor electrical panels, also known as outdoor electrical enclosures or control panels, are crucial components in various industrial, commercial, and residential applications. These panels house electrical equipment such as circuit breakers, fuses, switches, and relays, protecting them from environmental factors while ensuring safe and reliable operation. Manufacturing these panels requires a careful balance of design, material selection, and adherence to safety standards.
Design and Functionality
The design of outdoor electrical panels is critical to their functionality and durability. These panels must protect the internal components from harsh weather conditions, including rain, wind, dust, and extreme temperatures. Therefore, the design often includes features like waterproof seals, gaskets, and proper ventilation to prevent moisture build-up and overheating. The panels may also have lockable doors to ensure security and prevent unauthorized access.
Material Selection
Material selection plays a vital role in the manufacture of outdoor electrical panels. The most commonly used materials are:
-
Stainless Steel: Known for its corrosion resistance and durability, stainless steel is often used in harsh environments where the panel may be exposed to chemicals, saltwater, or other corrosive substances.
-
Aluminum: Lightweight and resistant to corrosion, aluminum is another popular choice. It is often used in applications where weight is a concern, such as on poles or structures where the panel needs to be mounted.
-
Polycarbonate and Fiberglass: These materials are used for panels that need to be lightweight, non-conductive, and resistant to UV radiation. They are ideal for outdoor applications where electrical insulation is crucial.
Manufacturing Process
The manufacturing process of outdoor electrical panels involves several stages:
-
Design and Engineering: The process begins with designing the panel according to the specific requirements of the application. This involves creating detailed drawings and selecting appropriate materials. Computer-aided design (CAD) software is often used to create precise designs and simulations.
-
Fabrication: Once the design is finalized, the material is cut, bent, and shaped into the desired form. For metal panels, this may involve processes like laser cutting, welding, and punching. Non-metallic panels may be molded or formed using different techniques.
-
Surface Treatment: To enhance durability, the panels may undergo surface treatments such as powder coating, anodizing, or painting. These treatments protect the material from corrosion and wear, extending the panel's lifespan.
-
Assembly: The next step involves assembling the panel with the necessary components, including mounting brackets, seals, and gaskets. Internal wiring and electrical components are also installed at this stage.
-
Testing and Quality Control: Once assembled, the panels undergo rigorous testing to ensure they meet safety and performance standards. This includes testing for water resistance, insulation integrity, and proper functioning of all electrical components.
-
Certification and Compliance: Outdoor electrical panels must comply with various standards and regulations, such as NEMA (National Electrical Manufacturers Association) ratings in the U.S., or IP (Ingress Protection) ratings internationally. These ratings indicate the panel's ability to withstand environmental conditions like dust and water.
Applications
Outdoor electrical panels are used in a wide range of applications, including:
- Industrial Automation: Controlling machinery and processes in manufacturing plants.
- Utilities: Housing control systems for power distribution, water treatment, and telecommunication networks.
- Renewable Energy: Protecting inverters, controllers, and other components in solar and wind power systems.
- Commercial Buildings: Managing lighting, HVAC systems, and other electrical loads.
- Residential Areas: Serving as main distribution panels or for specific outdoor electrical installations like lighting or pools.
Conclusion
The manufacture of outdoo
Contact : +91 99005 84314
Outdoor electrical panels, also known as outdoor electrical enclosures or control panels, are crucial components in various industrial, commercial, and residential applications. These panels house electrical equipment such as circuit breakers, fuses, switches, and relays, protecting them from environmental factors while ensuring safe and reliable operation. Manufacturing these panels requires a careful balance of design, material selection, and adherence to safety standards.
Design and Functionality
The design of outdoor electrical panels is critical to their functionality and durability. These panels must protect the internal components from harsh weather conditions, including rain, wind, dust, and extreme temperatures. Therefore, the design often includes features like waterproof seals, gaskets, and proper ventilation to prevent moisture build-up and overheating. The panels may also have lockable doors to ensure security and prevent unauthorized access.
Material Selection
Material selection plays a vital role in the manufacture of outdoor electrical panels. The most commonly used materials are:
-
Stainless Steel: Known for its corrosion resistance and durability, stainless steel is often used in harsh environments where the panel may be exposed to chemicals, saltwater, or other corrosive substances.
-
Aluminum: Lightweight and resistant to corrosion, aluminum is another popular choice. It is often used in applications where weight is a concern, such as on poles or structures where the panel needs to be mounted.
-
Polycarbonate and Fiberglass: These materials are used for panels that need to be lightweight, non-conductive, and resistant to UV radiation. They are ideal for outdoor applications where electrical insulation is crucial.
Manufacturing Process
The manufacturing process of outdoor electrical panels involves several stages:
-
Design and Engineering: The process begins with designing the panel according to the specific requirements of the application. This involves creating detailed drawings and selecting appropriate materials. Computer-aided design (CAD) software is often used to create precise designs and simulations.
-
Fabrication: Once the design is finalized, the material is cut, bent, and shaped into the desired form. For metal panels, this may involve processes like laser cutting, welding, and punching. Non-metallic panels may be molded or formed using different techniques.
-
Surface Treatment: To enhance durability, the panels may undergo surface treatments such as powder coating, anodizing, or painting. These treatments protect the material from corrosion and wear, extending the panel's lifespan.
-
Assembly: The next step involves assembling the panel with the necessary components, including mounting brackets, seals, and gaskets. Internal wiring and electrical components are also installed at this stage.
-
Testing and Quality Control: Once assembled, the panels undergo rigorous testing to ensure they meet safety and performance standards. This includes testing for water resistance, insulation integrity, and proper functioning of all electrical components.
-
Certification and Compliance: Outdoor electrical panels must comply with various standards and regulations, such as NEMA (National Electrical Manufacturers Association) ratings in the U.S., or IP (Ingress Protection) ratings internationally. These ratings indicate the panel's ability to withstand environmental conditions like dust and water.
Applications
Outdoor electrical panels are used in a wide range of applications, including:
- Industrial Automation: Controlling machinery and processes in manufacturing plants.
- Utilities: Housing control systems for power distribution, water treatment, and telecommunication networks.
- Renewable Energy: Protecting inverters, controllers, and other components in solar and wind power systems.
- Commercial Buildings: Managing lighting, HVAC systems, and other electrical loads.
- Residential Areas: Serving as main distribution panels or for specific outdoor electrical installations like lighting or pools.
Conclusion
The manufacture of outdoor electrical panels is a complex process that requires attention to detail, quality materials, and adherence to safety standards. These panels are essential for protecting electrical systems in various environments, ensuring reliability and safety. With advancements in technology and materials, outdoor electrical panels continue to evolve, offering improved performance and durability for a wide range of applications.
r electrical panels is a complex process that requires attention to detail, quality materials, and adherence to safety standards. These panels are essential for protecting electrical systems in various environments, ensuring reliability and safety. With advancements in technology and materials, outdoor electrical panels continue to evolve, offering improved performance and durability for a wide range of applications.